[Chinese Packaging Network News] In today's business landscape, our products have rapidly changed from price and service competing strategies to quality-based corporate products to dominate the market, especially in today's corporate production costs, The continuous increase in labor costs and the diversified demands of customers' products, and the increasing importance of product quality in the competitive landscape of the industry, can be said that if your products do not attach importance to quality, even if your products currently occupy a place in the market However, in the end it will inevitably be eliminated. Quality is always the core competitive power of a company. It is one of the cores of corporate brand building. It is an enterprise's development and market expansion, and the trust of the customers trusts! How to bring this edge into full play is a problem that our soft packaging companies are thinking about, a goal pursued by our soft pack companies, and a question we need to discuss today.
One we must do a good job of quality management monitoring
First of all, we must know what is quality? Quality: The degree to which a set of inherent characteristics meet customer requirements. Characteristics (size, appearance, performance, composition, structure), etc.
Second, quality consciousness. Quality awareness: refers to the perception of quality by production and quality control personnel. This perception must be strong, as reflected in the details of the work.
The production and operation standards of the workshop and the establishment and implementation of the internal quality control system for each workshop. SOP (standard operation)
The establishment of a quality system. system. Generally refers to a set of interrelated, interactive elements, or a system that consists of several elements. This "organic" mainly refers to the meaning of mutual connection, mutual action and mutual supervision. (ISO9000 Quality System Certification, Implementation and Innovation of Standard Processes, Design and Analysis of Prenatal Products)
Total Quality Management (TQM) implementation and promotion. Quality of everyone, everyone is a quality controller!
II: On-site Quality Management Process Control
[pagebreak]
Our flexible packaging company's production workshop generally consists of printing, recycling, distribution, system, and four links to carry out the flow system operation. Then we know that the five major elements involved in quality management are people, machines, materials, methods, and rings. The reason why people are placed first is because quality is produced and controlled by people. Many times we all know the quality management method of PDCA, but the key is how to do it consistently, which is very important. So how do you manage quality control at the site? I will discuss the following aspects.
The on-site quality management control emphasizes fast, accurate and accurate. Fast is the production personnel and quality control personnel. The speed of finding quality problems and potential quality problems at the site must be fast, or if there is no quality problem, we must have this quality consciousness, and then discover quality problems or potential quality. Judgment should be timely and accurate, reduce mistakes, and finally there should be two interpretations. First, the meaning of the embarrassment is to strictly control the quality of on-site management, strict requirements on their own job responsibilities, high standards, high requirements, and implementation. Strong, summed up as their own, and second, the operator of the production line in the production of the quality of non-compliance, from the strict requirements, standardize the quality of operating procedures. If the quality control personnel have insufficient quality requirements for themselves and the production line, the final result will be uncomfortable for the company, and even the entire order may be lost. In this regard, we first talk about a case where we once produced products with golden text. When the first one was confirmed, the color was wrong. At that time, the on-duty printing engineer said that he could adjust it. The result was a first roll of the machine. No, quality inspectors said they couldn't do it. To stop the process, the captain said that this could be adjusted well and the result was adjusted again. (The panicked operator took the wrong hue of the ink.) The treatment was too late and a large number of defective products appeared. From this analysis, we can conclude that the quality control personnel's judgment on the quality problem is not accurate enough. The captain of the flight is not aware of it, but he is holding the psychological boot of the fluke, and the quality awareness is not strong enough. The implementation of on-site quality control personnel is not Strong, causing the emergence of quality problems, this is the result of the above-mentioned lack of embarrassment.
On-site quality control process management site quality control, pay attention to the source control, that is, raw material quality control, stable raw material is the premise of product quality control. Our general quality control can be divided into: IQC (inspection), LQC (inspection inspection), PQC (process inspection), OQC (finished product shipment inspection), QA (quality control management), etc. Part of the composition, these links must be closely integrated, use PDCA's quality cycle management to operate, form a quality management circle, to enhance the quality control of the entire quality control department.
IQC source quality management requires that we conduct scientific random inspection and testing of incoming materials, carry out spot checks according to raw material inspection standards, and directly feedback the quality information of first-hand raw materials, which can effectively avoid the loss caused by raw material quality problems. Such as the uneven thickness of the material, if it can be detected in the material inspection, it can avoid the problem of wrinkling and poor quality of overprinting during production.
LQC inspection, before we say quality control patrol, we first talk about a case. When we were producing a three-sided outer bag, the bag captain did not look at the process card before production and used his own experience. Production, the size of the bag top seal position, the original required top seal 2CM made 3CM, on-site patrollers have to do the first confirmation, but did not do detailed, only measured the bag wide bag length, not measured The size and specifications of the top seal did not look at the process card. Afterwards, the captain did not see the process card for production (because the craftman did not send it down in time). The inspector did not look at it and did not measure it. The inspection items on the first report found that there was no clear requirement for dimensional inspection and it was very general. These parts formed the final result of the above quality accident and scrapped 5000 bags! Inspection is critical, we usually require that the inspectors must have information on the quality of the products that they need to produce, such as production orders, processes, product quality control plans, and all points of product quality prevention and control before production. Full control will help control production. Before the production, we must ask for the first confirmation work. How this work is done relates to the quality control of the entire product. The first confirmation is that the production and quality control parties shall carry out uniform confirmation and confirmation according to quality control standards and systems. The project includes a variety of product quality parameters and requirements, such as plate roller text pattern, hue, adhesion and other requirements to achieve the next step in the production work, this link is critical. Many times our product quality problems are related to this link. How to do a good job in this aspect of control is to say "squeak" before. Only in this way can we reduce the difficulty of subsequent quality control. After completing the first confirmation, LQC started the work. The next step was to supervise the operator of the workshop to perform the required operation according to requirements. The more important point was the continuous inspection and monitoring of the quality of the on-line production products, and the discovery of problems and advances. Feedback on-duty personnel, and follow up the improved product quality results, and work closely with the production staff to do quality work. The job of this position requires quality inspectors to have certain requirements in terms of considerable work experience, as well as knowledge of flexible packaging products and on-site quality control methods.
[pagebreak]
PQC is also called rewinding and quality inspection. The main requirement of this quality control link is that the quality inspector must be serious and have the relevant printing knowledge and the ability to judge and identify print quality problems. We usually use the second look, more than three methods, more stop, more observation, more careful, a look at the membrane head, and second look at the membrane tail. The problem was found to be handled according to quality requirements. If the quality control is fine, it can control the loss of the printing shop. This place can account for about 20% of the printing waste rate, which means that printing can be reduced by 15% in performance evaluation. About loss.
This link is the assembly point of the entire quality and is the last line of defense to ensure product quality. All products with quality problems will be blocked within this line of defense. The quality of products monitored at this stage will be considered as meeting the customer's product quality requirements and standards. Therefore, the link directly faces the customer, so this quality control personnel must have enough The patience, meticulousness, and sense of responsibility are also part of the process of testing the quality control of the product's entire production process.
Raw materials. A stable raw material supplier can effectively increase the quality of the product, which can effectively reduce many losses. The quality of raw materials directly determines the stability of product quality. Some companies have to reduce costs, which one is cheaper to use, this is undesirable, and quality control is even less controllable.
Process. The product quality comes from the continuous improvement of the production process, and the stable production process produces production, which can effectively reduce the occurrence of quality problems. Of course, it should be noted that the production line operators need to effectively and accurately execute the production process parameters. This is a critical and important link. Some companies have written very well in terms of craftsmanship, but in the production process, they have not gone through the process of operation and are left aside. This is formalism. Did not really implement it. Some companies still do not have quality management at all, and the production of process cards can be said to be a bottleneck for the quality of many companies.
Product quality control. In general, the entire production, procurement, and quality control departments need to work together to carry out quality summarization and analysis from time to time, with a focus on prevention and solving supplementary work modes, and using standard operating procedures of the SOP to standardize operations. Standards, high requirements, high efficiency and complete quality control work, all work has been the core of product quality as a prerequisite for production, coupled with a good executive management team, can effectively improve product quality to a new level .
Establishment of corporate standards. Many companies now have almost no corporate standards, and some rely more on experience to produce. Enterprises on a certain scale must have enterprise standards and national standards to control the quality of their production products. Therefore, the establishment of enterprise standards is a matter of enterprises. Summarizing the quality information, further improving and stabilizing product quality, finding out the shortcomings in the existing quality information, and adding guidance from the national standard, can effectively improve the adaptability of the product quality of the enterprise standard, and gradually meet the requirements of the national standard. Make product quality more stable.
Carry out ISO quality system certification. When these aspects are mature enough, we must carry out the ISO quality system certification work, it can not only effectively consolidate the existing quality management, but also can improve the existing quality management, can further standardize the quality management work, The original quality management is more organized, standardized and scientific. It will fundamentally change the enterprise quality management and production management, reach a new height, and the certification of the quality system will further enhance the quality image of the company and enhance the competitiveness of the enterprise market. Improving customer satisfaction and building corporate branding have become the core of corporate culture construction.
One we must do a good job of quality management monitoring
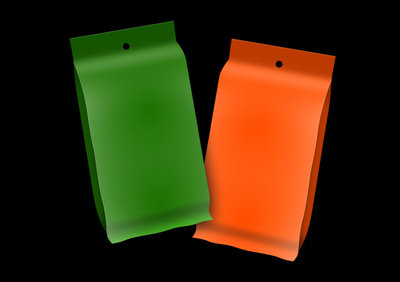
Second, quality consciousness. Quality awareness: refers to the perception of quality by production and quality control personnel. This perception must be strong, as reflected in the details of the work.
The production and operation standards of the workshop and the establishment and implementation of the internal quality control system for each workshop. SOP (standard operation)
The establishment of a quality system. system. Generally refers to a set of interrelated, interactive elements, or a system that consists of several elements. This "organic" mainly refers to the meaning of mutual connection, mutual action and mutual supervision. (ISO9000 Quality System Certification, Implementation and Innovation of Standard Processes, Design and Analysis of Prenatal Products)
Total Quality Management (TQM) implementation and promotion. Quality of everyone, everyone is a quality controller!
II: On-site Quality Management Process Control
[pagebreak]
Our flexible packaging company's production workshop generally consists of printing, recycling, distribution, system, and four links to carry out the flow system operation. Then we know that the five major elements involved in quality management are people, machines, materials, methods, and rings. The reason why people are placed first is because quality is produced and controlled by people. Many times we all know the quality management method of PDCA, but the key is how to do it consistently, which is very important. So how do you manage quality control at the site? I will discuss the following aspects.
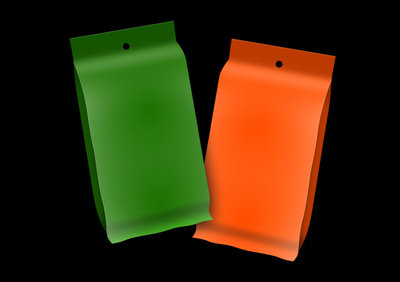
On-site quality control process management site quality control, pay attention to the source control, that is, raw material quality control, stable raw material is the premise of product quality control. Our general quality control can be divided into: IQC (inspection), LQC (inspection inspection), PQC (process inspection), OQC (finished product shipment inspection), QA (quality control management), etc. Part of the composition, these links must be closely integrated, use PDCA's quality cycle management to operate, form a quality management circle, to enhance the quality control of the entire quality control department.
IQC source quality management requires that we conduct scientific random inspection and testing of incoming materials, carry out spot checks according to raw material inspection standards, and directly feedback the quality information of first-hand raw materials, which can effectively avoid the loss caused by raw material quality problems. Such as the uneven thickness of the material, if it can be detected in the material inspection, it can avoid the problem of wrinkling and poor quality of overprinting during production.
LQC inspection, before we say quality control patrol, we first talk about a case. When we were producing a three-sided outer bag, the bag captain did not look at the process card before production and used his own experience. Production, the size of the bag top seal position, the original required top seal 2CM made 3CM, on-site patrollers have to do the first confirmation, but did not do detailed, only measured the bag wide bag length, not measured The size and specifications of the top seal did not look at the process card. Afterwards, the captain did not see the process card for production (because the craftman did not send it down in time). The inspector did not look at it and did not measure it. The inspection items on the first report found that there was no clear requirement for dimensional inspection and it was very general. These parts formed the final result of the above quality accident and scrapped 5000 bags! Inspection is critical, we usually require that the inspectors must have information on the quality of the products that they need to produce, such as production orders, processes, product quality control plans, and all points of product quality prevention and control before production. Full control will help control production. Before the production, we must ask for the first confirmation work. How this work is done relates to the quality control of the entire product. The first confirmation is that the production and quality control parties shall carry out uniform confirmation and confirmation according to quality control standards and systems. The project includes a variety of product quality parameters and requirements, such as plate roller text pattern, hue, adhesion and other requirements to achieve the next step in the production work, this link is critical. Many times our product quality problems are related to this link. How to do a good job in this aspect of control is to say "squeak" before. Only in this way can we reduce the difficulty of subsequent quality control. After completing the first confirmation, LQC started the work. The next step was to supervise the operator of the workshop to perform the required operation according to requirements. The more important point was the continuous inspection and monitoring of the quality of the on-line production products, and the discovery of problems and advances. Feedback on-duty personnel, and follow up the improved product quality results, and work closely with the production staff to do quality work. The job of this position requires quality inspectors to have certain requirements in terms of considerable work experience, as well as knowledge of flexible packaging products and on-site quality control methods.
[pagebreak]
PQC is also called rewinding and quality inspection. The main requirement of this quality control link is that the quality inspector must be serious and have the relevant printing knowledge and the ability to judge and identify print quality problems. We usually use the second look, more than three methods, more stop, more observation, more careful, a look at the membrane head, and second look at the membrane tail. The problem was found to be handled according to quality requirements. If the quality control is fine, it can control the loss of the printing shop. This place can account for about 20% of the printing waste rate, which means that printing can be reduced by 15% in performance evaluation. About loss.
This link is the assembly point of the entire quality and is the last line of defense to ensure product quality. All products with quality problems will be blocked within this line of defense. The quality of products monitored at this stage will be considered as meeting the customer's product quality requirements and standards. Therefore, the link directly faces the customer, so this quality control personnel must have enough The patience, meticulousness, and sense of responsibility are also part of the process of testing the quality control of the product's entire production process.
Raw materials. A stable raw material supplier can effectively increase the quality of the product, which can effectively reduce many losses. The quality of raw materials directly determines the stability of product quality. Some companies have to reduce costs, which one is cheaper to use, this is undesirable, and quality control is even less controllable.
Process. The product quality comes from the continuous improvement of the production process, and the stable production process produces production, which can effectively reduce the occurrence of quality problems. Of course, it should be noted that the production line operators need to effectively and accurately execute the production process parameters. This is a critical and important link. Some companies have written very well in terms of craftsmanship, but in the production process, they have not gone through the process of operation and are left aside. This is formalism. Did not really implement it. Some companies still do not have quality management at all, and the production of process cards can be said to be a bottleneck for the quality of many companies.
Product quality control. In general, the entire production, procurement, and quality control departments need to work together to carry out quality summarization and analysis from time to time, with a focus on prevention and solving supplementary work modes, and using standard operating procedures of the SOP to standardize operations. Standards, high requirements, high efficiency and complete quality control work, all work has been the core of product quality as a prerequisite for production, coupled with a good executive management team, can effectively improve product quality to a new level .
Establishment of corporate standards. Many companies now have almost no corporate standards, and some rely more on experience to produce. Enterprises on a certain scale must have enterprise standards and national standards to control the quality of their production products. Therefore, the establishment of enterprise standards is a matter of enterprises. Summarizing the quality information, further improving and stabilizing product quality, finding out the shortcomings in the existing quality information, and adding guidance from the national standard, can effectively improve the adaptability of the product quality of the enterprise standard, and gradually meet the requirements of the national standard. Make product quality more stable.
Carry out ISO quality system certification. When these aspects are mature enough, we must carry out the ISO quality system certification work, it can not only effectively consolidate the existing quality management, but also can improve the existing quality management, can further standardize the quality management work, The original quality management is more organized, standardized and scientific. It will fundamentally change the enterprise quality management and production management, reach a new height, and the certification of the quality system will further enhance the quality image of the company and enhance the competitiveness of the enterprise market. Improving customer satisfaction and building corporate branding have become the core of corporate culture construction.
Ruijie Plastic Machinery Co., Ltd. , http://www.vulcanizingpress.com