The amount of fountain solution and alcohol is set correctly, but it often dries. What could be the reason?
In the lithographic printing process, the so-called "dry" means that the blank part of the printing plate does not form a sufficiently uniform water film, ie, the amount of water in the non-image part on the printing plate is insufficient. Once the offset printing plate is exposed to water, it will cause the blank part of the printing plate to be dirty, which will affect the quality of the printed product. In other words, the balance of ink and ink will be out of control during the printing process.
In the offset printing process, the control of the ink balance is related to many factors, including the adjustment ratio of the ink volume and the water volume, the quality of the fountain solution itself, the concentration of the fountain solution, the amount and temperature of the alcohol, the nature of the ink itself, and the pressure of the ink roller. , environmental temperature and humidity and so on.
If the amount of fountain solution and the amount of alcohol used in the printing process are correct, the reason why the printing plate is dried may be caused by improper setting of the ink supply roller of the ink supply system and the water roller pressure of the water supply system during the printing process. It is related to the quality of the fountain solution used in the printing process.
If the printing pressure between the ink roller and the printing plate of the ink supply system is too large, the abrasion of the sand in the blank part of the printing plate will be accelerated, resulting in a decrease in the hydrophilicity of the non-image part of the printing plate, so that the blank part of the printing plate is in the original Under the conditions of water supply, it is not possible to obtain enough water, and water-drying of the plate layout occurs.
If the pressure between the ink form roller and the printing plate in the ink supply system is set correctly, water-drying still occurs, which may be caused by improper pressure setting between the water rollers in the water supply system. Especially when using an alcohol fountain solution, since the surface tension of the alcohol fountain solution is low and the spreadability is good, a small amount of dampening solution in the blank portion of the printing plate can form a uniform water film, thereby greatly reducing the Layout water supply. Therefore, the pressure between the water rollers is insufficient and it is more likely to cause the dry plate phenomenon. On the other hand, if there is oil on the water roller, it will also affect the water supply volume of the water roller, which will lead to water and dry failure of the plate layout.
Even if the amount of fountain solution and alcohol used in the printing process is set correctly, it does not mean that the quality of the used fountain solution is stable. The fountain solution should also have buffering properties for pH, plate protection, wettability, corrosion protection, bactericidal properties, and antifoam properties. The buffer in the fountain solution is mainly used to stabilize the pH of the fountain solution because the fountain solution is generally acidic. As the amount of buffer added, the pH of the fountain solution will fluctuate more. Improper amount will affect the hydrophilic properties of the printing plate. The protective performance of the printing plate refers to the protection of the hydrophilic properties of the printing plate. If it is used improperly, it will also reduce the hydrophilic properties of the printing plate and cause water-drying. The bactericide can prevent algae and microorganisms from breeding in the water circulation system and avoid clogging of pipelines. The anti-foaming agent can prevent the formation of bubbles and prevent the large amount of foam in the water tank from being detrimental to the wetting of the printing plate.
Therefore, when water-drying occurs during offset printing, it is necessary to first check whether the pressure setting between the ink roller and the water roller is correct, and at the same time, clean the water roller regularly. In addition, high-quality fountain solution must be selected during the printing process. When selecting the fountain solution, the user should combine the water quality and other conditions of the printing plant to strictly control the amount of fountain solution added, isopropyl alcohol ( The amount of alcohol added, the pH of the fountain solution, and the conductivity.
From the above analysis, it can be seen that the dampening solution is the most important factor in the water-dry failure during the offset printing process besides the printing plate and the ink-on-water system. Even if the amount of alcohol in the fountain solution and the usage amount of the fountain solution are set. All of them are correct, and offset water drying may also occur due to other factors.
In the lithographic printing process, the so-called "dry" means that the blank part of the printing plate does not form a sufficiently uniform water film, ie, the amount of water in the non-image part on the printing plate is insufficient. Once the offset printing plate is exposed to water, it will cause the blank part of the printing plate to be dirty, which will affect the quality of the printed product. In other words, the balance of ink and ink will be out of control during the printing process.
In the offset printing process, the control of the ink balance is related to many factors, including the adjustment ratio of the ink volume and the water volume, the quality of the fountain solution itself, the concentration of the fountain solution, the amount and temperature of the alcohol, the nature of the ink itself, and the pressure of the ink roller. , environmental temperature and humidity and so on.
If the amount of fountain solution and the amount of alcohol used in the printing process are correct, the reason why the printing plate is dried may be caused by improper setting of the ink supply roller of the ink supply system and the water roller pressure of the water supply system during the printing process. It is related to the quality of the fountain solution used in the printing process.
If the printing pressure between the ink roller and the printing plate of the ink supply system is too large, the abrasion of the sand in the blank part of the printing plate will be accelerated, resulting in a decrease in the hydrophilicity of the non-image part of the printing plate, so that the blank part of the printing plate is in the original Under the conditions of water supply, it is not possible to obtain enough water, and water-drying of the plate layout occurs.
If the pressure between the ink form roller and the printing plate in the ink supply system is set correctly, water-drying still occurs, which may be caused by improper pressure setting between the water rollers in the water supply system. Especially when using an alcohol fountain solution, since the surface tension of the alcohol fountain solution is low and the spreadability is good, a small amount of dampening solution in the blank portion of the printing plate can form a uniform water film, thereby greatly reducing the Layout water supply. Therefore, the pressure between the water rollers is insufficient and it is more likely to cause the dry plate phenomenon. On the other hand, if there is oil on the water roller, it will also affect the water supply volume of the water roller, which will lead to water and dry failure of the plate layout.
Even if the amount of fountain solution and alcohol used in the printing process is set correctly, it does not mean that the quality of the used fountain solution is stable. The fountain solution should also have buffering properties for pH, plate protection, wettability, corrosion protection, bactericidal properties, and antifoam properties. The buffer in the fountain solution is mainly used to stabilize the pH of the fountain solution because the fountain solution is generally acidic. As the amount of buffer added, the pH of the fountain solution will fluctuate more. Improper amount will affect the hydrophilic properties of the printing plate. The protective performance of the printing plate refers to the protection of the hydrophilic properties of the printing plate. If it is used improperly, it will also reduce the hydrophilic properties of the printing plate and cause water-drying. The bactericide can prevent algae and microorganisms from breeding in the water circulation system and avoid clogging of pipelines. The anti-foaming agent can prevent the formation of bubbles and prevent the large amount of foam in the water tank from being detrimental to the wetting of the printing plate.
Therefore, when water-drying occurs during offset printing, it is necessary to first check whether the pressure setting between the ink roller and the water roller is correct, and at the same time, clean the water roller regularly. In addition, high-quality fountain solution must be selected during the printing process. When selecting the fountain solution, the user should combine the water quality and other conditions of the printing plant to strictly control the amount of fountain solution added, isopropyl alcohol ( The amount of alcohol added, the pH of the fountain solution, and the conductivity.
From the above analysis, it can be seen that the dampening solution is the most important factor in the water-dry failure during the offset printing process besides the printing plate and the ink-on-water system. Even if the amount of alcohol in the fountain solution and the usage amount of the fountain solution are set. All of them are correct, and offset water drying may also occur due to other factors.
Cailang specialized in making Corrugated Paper Box for over 24 years. With our own factory, help to stay at cost level, but in high quality. Corrugated Boxes is not only to protect the products during shipping, also do a great help to speak out your own brand. With perfect after-sales service, we will always be here waiting for you!
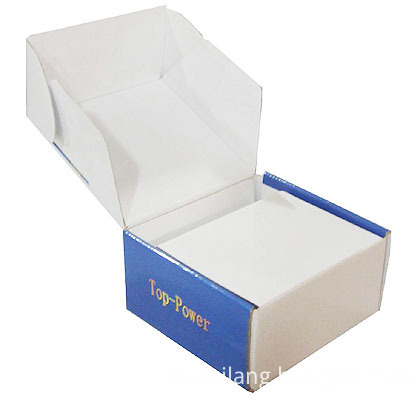
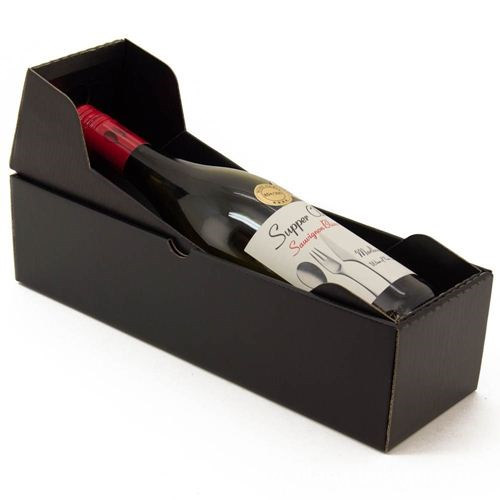
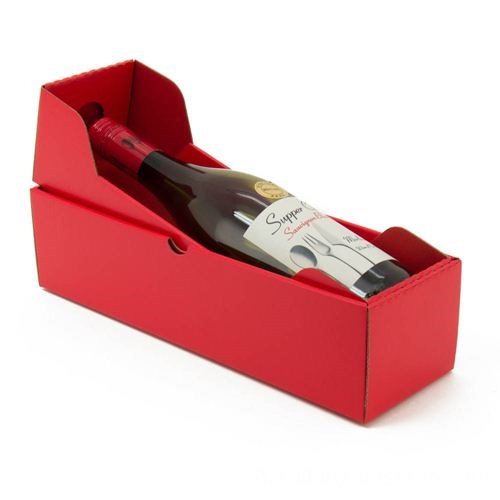
Corrugated Paper Box
Corrugated Paper Box,Recyclable Corrugated Paper Box,Paper Corrugated Carton Box,Corrugated Paper Shipping Box
Huizhou Cailang Printing Products Co.,Ltd. , https://www.paperboxs.nl