With the development of social economy and the improvement of people’s living standards, people are paying more and more attention to the perfection of commodity packaging. Corrugated carton packaging has a growing share of the entire packaging industry with its unique features. The key technology of corrugated cartons lies in the printing of ink and ink. This article talks about how to use the equipment improvement to improve the quality of ink printing.
1 Printing dew spot treatment
Printing mottled white spots is the most common and most difficult quality problem in corrugated box production. The reasons for this are: 1) poor ink absorption performance of the paper; 2) dirty offset plates; 3) paper scraps and dust on the cardboard. One of the traditional methods of dealing with these problems is to change the box manually, and second, to increase the frequency of the artificial eraser. These methods will play a role in the objective. However, the effect of the change in the box is not improved, and the efficiency is reduced. The wiping of rubber also causes waste of water, electricity, and labor.
In the process of equipment installation, maintenance and management, I have observed through long-term observation and analysis that the key to causing dew-white spots is dust, and the main source of dust is the single-pitch sub-paper. Based on this situation, I installed electrostatic suction devices on the back end of the computer cross cutter of the cardboard production line and the paper feeding section of the press two years ago. Use a hair dryer in front of the computer to cut the knife. When the paper is separated from the single knife, the paper hidden in the pit pattern is smashed or blown off. Then, the paper is crushed by the electrostatic dust collector at the delivery rack after the computer crosses the knife. Suck away. In the paper feeding section of the printing press, the dust on the paperboard is sucked away by the electrostatic dust at the aprons of the paper feeding aprons and the feed rollers, so as to keep the printing surface clean and dust free, so that when the product enters the printing roller, ink is not disturbed and the ink is sucked. Uniform.
After such improvements, the printing effect of the product is significantly improved, and the phenomenon of dew-white spots caused by dust is fundamentally prevented.
2 sets of stamped bit processing
Nowadays, more and more attention has been paid to the artistic and three-dimensional appearance of the patterns in the packaging of goods so that consumers can feel the perfection of the purchased goods from the packaging. To achieve this goal, packaging printing must use multi-color printing - that is, multicolor printing.
In the overprinting process, there is often the occurrence of misalignment between the latter color and the previous color superposition or the positioning position, resulting in the printing pattern can not reflect the design effect of the product packaging, and even a great deal of confusion, damaged the product's image.
In response to this particular problem, I went through a period of in-depth field investigation and study, from the electronic control reaction speed to the precision of the mechanical fit tolerance, carried out a detailed calculation, carried out several improvements on the existing equipment, and developed related equipment maintenance Measures.
1) Improve the accuracy of the phase positioning of the plate cylinder
The phase position of the plate cylinder is controlled by encoder and counter. If the precision of counter is too low, the position of encoder is inaccurate and the position of the printer is shifted. The common counter reaction speed is 3K, but it often produces an error of ±1mm during positioning. After consultation with Taiwan Electric Control Co., Ltd., a 5K counter is produced, and the positioning error is reduced to 0.4mm.
2) Timed lubrication and detection of transmission machinery
In the paper feeding process, if the transmission machinery can not maintain a good and smooth operation, the position of each paper board arrives will change, resulting in overprinting. Therefore, it is very important to properly maintain and test the equipment. We have developed a daily commissioning checklist before starting work, including lubrication and maintenance. At the same time, the limits for wear of feed rollers and feed rollers are set. If they fail to pass, they must be turned and re-wrapped or replaced to overcome the phenomenon of walking and oblique movement of the cardboard during walking.
3) Using suction to feed paper
The traditional printing press adopts the upper printing, and only the paper-receiving wheel can be used to convey the paperboard, while the new printing press adopts the advanced technology of lower printing and upper suction air conveying cardboard. The suction paper feed uses the wind to suck the cardboard on the transfer wheel. The suction force is uniform, the position is not taken, and the position is not inclined, and the bent cardboard is leveled. When printing, the position is level and the ink is evener.
3 Printing ink bad treatment
Ink problems In addition to paper problems and offset problems, there are technical problems with the ink roller on the equipment.
Ink rollers adopt anilox rollers. In the high standard carton printing, anilox rollers with more than 250 lines are used. The mesh holes are easily blocked by the ink residue, resulting in uneven ink application, insufficient ink, and light ink. The traditional method is to use clean water, no Na water scrub or scrubbing scrubbing and other methods, but the effect is not ideal, a new inking roller life less than a month, the effect is significantly inferior.
Through long-term trial and error experiments, we feel that the following methods can effectively solve the problem of poor printing ink.
1) Add a filter in the ink tank to prevent the ink particles from entering the ink roller.
2) Use an anilox deep cleaner for cleaning on a regular (usually half month) basis?
3) Wash the ink roller with clean water circulation at work everyday, and inspect the mesh of the ink roller with a magnifying glass 60 times to 100 times. No residue of the ink residue, such as residual ink residue, immediately clean with a deep cleaning agent.
Through the above points of maintenance, the inking ink roller effect will always be good.
The above-mentioned several printing technical problems are crucial to the quality of the carton products in actual production. Through the recognition and improvement of the equipment and good maintenance, the products that the customer is satisfied with can be produced and the comprehensive benefits of the enterprise can be improved.
This is a good machine for making twisted paper ropes in roll, you can use the twisted ropes to wrap the gifts or for craft products, paper handle after knotted or tipped at the two ends or you can use it on the Paper Handle making to make different paper handles. It is running stably and fast and the rope diameters can be different and adjustable and customized according to customers` request. The rope can be made in different ways by using one paper roll, 2 rolls or more, which depends on the rope tightness, strongness, roundness and colors
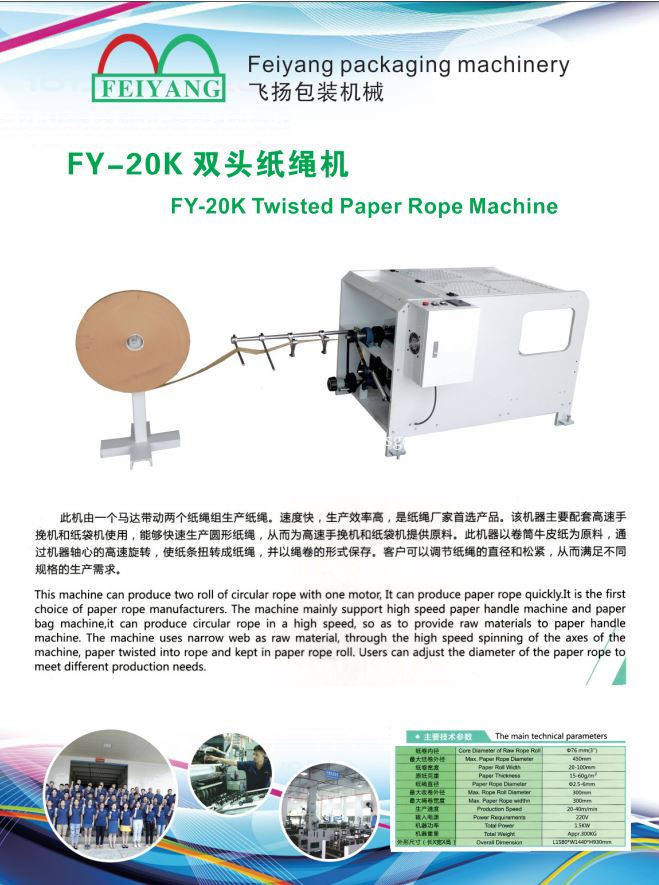
Single Head Paper Rope Making Machine
paper rope, paper cord, paper rope making machine, paper cord making machine, paper rope machine, paper cord machine
DongGuan FeiYang Packaging Machinery Equipment Co., Ltd , http://www.feiyang-machinery.com